The Growing Importance of Fuel Efficiency in Steam Boilers
In today’s industrial landscape, steam boiler diesel consumption has become a critical factor for businesses seeking to balance operational costs with environmental responsibility. As fuel prices fluctuate and environmental regulations tighten, manufacturers across various sectors are increasingly focused on reducing their steam boiler diesel consumption while maintaining optimal production output. The food and beverage industry, in particular, faces unique challenges where steam quality directly impacts product characteristics while energy efficiency affects bottom-line profitability.
Advanced Steam Boiler Technologies for Reduced Diesel Consumption
Modern boiler manufacturers have responded to these challenges by developing innovative solutions that dramatically lower steam boiler diesel consumption. Two prominent series, the WNS and SZS steam boilers, represent significant advancements in this field. These designs incorporate advanced combustion technology and heat recovery systems that maximize thermal efficiency while minimizing fuel requirements. Their intelligent control systems continuously monitor and adjust operations to maintain optimal steam boiler diesel consumption under varying load conditions.
Technical Specifications and environmental advantages of WNS Series Steam Boilers
The WNS series steam boilers feature a three-pass wet-back design that achieves remarkable thermal efficiency up to 98%. This exceptional performance directly translates to reduced steam boiler diesel consumption compared to conventional models. Key components like corrugated furnace tubes and threaded smoke tubes enhance heat transfer efficiency, while special furnace insulation material reduces heat loss. The series incorporates advanced condensing technology that recovers waste heat from exhaust gases, further improving fuel utilization and lowering steam boiler diesel consumption.
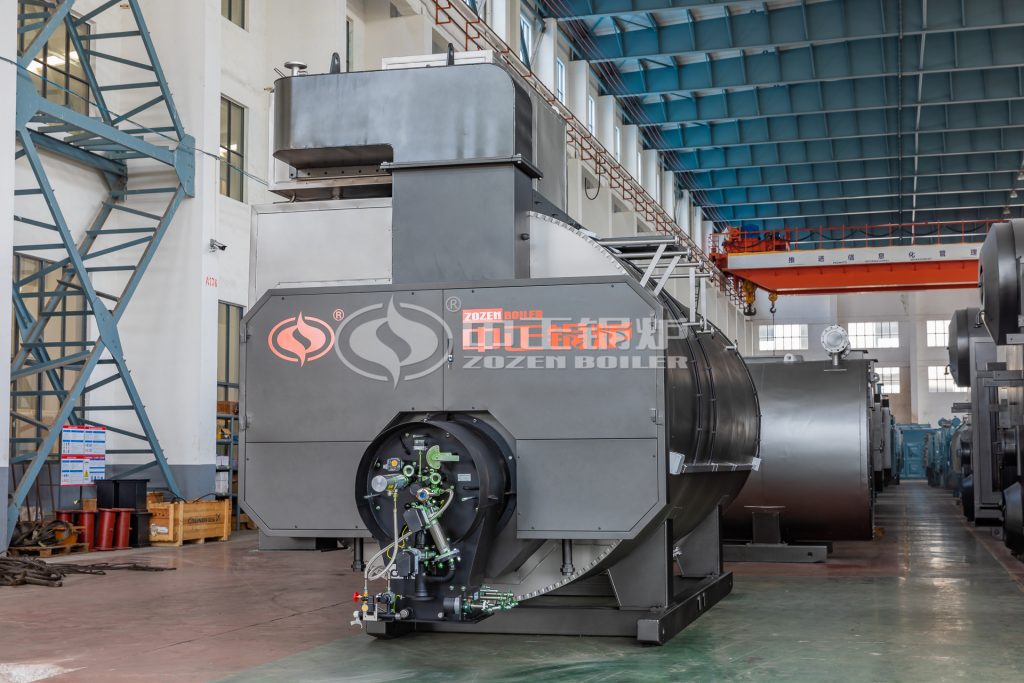
Steam Boiler Diesel Consumption
The SZS series represents another leap forward in efficient steam generation with its water-tube design and large furnace volume. These boilers achieve ultra-low NOx emissions below 30mg/m³ while maintaining excellent fuel efficiency. The membrane water-cooled wall structure ensures complete combustion and maximum heat absorption, significantly reducing steam boiler diesel consumption. Automatic control systems optimize the air-fuel ratio in real-time, ensuring clean combustion with minimal excess air that could otherwise waste energy.
Case Study: Distillery Application Demonstrates Efficiency Gains
A prominent baijiu producer in Zhejiang province provides an excellent case study of these efficiency improvements in practice. Facing production expansion to 500,000 kilograms annually, the distillery required a steam solution that could meet rigorous quality standards while controlling steam boiler diesel consumption. The installation of a 2-ton condensing WNS series gas-fired steam boiler delivered exceptional results across several key performance indicators.
Operational Benefits and High Efficiency of ZOZEN WNS Steam Boiler
The steam boiler’s high-efficiency condensing technology recovered substantial heat from exhaust gases, reducing steam boiler diesel consumption compared to conventional systems. This translated directly to lower operating costs without compromising the stable steam supply critical for consistent distillation quality. The boiler’s precise temperature control and rapid response to load changes ensured optimal conditions throughout the production cycle, demonstrating how advanced steam technology can enhance both efficiency and product quality simultaneously.
Beyond economic benefits, the steam boiler’s environmental performance proved equally impressive. The low-NOx combustion system maintained emissions well below regulatory limits, addressing growing concerns about industrial air pollution. By minimizing steam boiler diesel consumption, the system also reduced the distillery’s overall carbon footprint – an increasingly important consideration for environmentally conscious consumers and regulators alike. These sustainability benefits complemented the operational advantages, creating a compelling business case for the technology upgrade.The boiler’s automated control system not only optimized steam boiler diesel consumption but also simplified operation and enhanced safety.
While the distillery case highlights WNS steam boiler’s benefits for alcohol production, similar efficiency gains apply across food processing, pharmaceuticals, textiles, and other steam-intensive industries. The principles of reduced steam boiler diesel consumption through advanced combustion technology, heat recovery systems, and intelligent controls have universal relevance. Companies evaluating boiler upgrades should consider both immediate fuel savings and long-term operational benefits when assessing these modern systems.
Conclusion: The Future of Efficient Steam Generation
As industries worldwide face increasing pressure to improve sustainability while maintaining competitiveness, optimizing steam boiler diesel consumption will remain a priority. The demonstrated success of high-efficiency condensing boilers in demanding applications like distillation proves the technology’s reliability and economic viability. Future developments will likely push thermal efficiency even higher while further reducing emissions, continuing the trend of doing more with less energy input. For businesses seeking to modernize their steam systems, ZOZEN boiler represents a smart investment that pays dividends in both operational performance and environmental stewardship.